In close cooperation with MAN D&T’s licensees over the past few years, the first alternative fuel burning engine, the ME-GI engine, has been matured from extensive testing on numerous ME-GI engines on the test bed.
At the same time, the functionality of the auxiliary and fuel gas supply systems (FGSS) has been validated.The most recent development of the ME-GI engine is based on the experience gained from operating on natural gas on a number of commercial vessels in service.The ME-LGI injection concept was developed in parallel with the above. This new injection concept expands MAN D&T’s Dual Fuel two-stroke portfolio and enables the exploitation of more low flashpoint fuels such as Methanol, Ethanol and LPG (liquid petroleum gas) – all fuels which behave in a similar way as liquid fuels when injected. In this respect, the ability of the ME-LGI engine to run on these Sulphur-free fuels offers great potential for ship operation within SECA zones.
The ME-LGI engine benefits from electronic controls that encompass the fuel being injected by a so-called fuel booster injection valve (FBIV). This innovative fuel booster, specially developed for the ME-LGI engine, ensures that a low-pressure fuel-gas supply system can be employed.The first inquiries regarding application of this technology concerned Methanol and LPG carriers having operated at sea for many years with conventional fuel-burning engines. Many more LPG tankers are currently being built as global LPG infrastructure grows. Therefore, with a viable, convenient and comparatively cheap fuel already on board, it makes sense to save time for bunkering by using a fraction of the cargo to power the vessel with an important side benefit being the environmental benefits.
The development of ME-LGI for operation on Methanol is already completed, and the first vessels in a series of 50,000 dwt Methanol carriers entered service in Q2 2016, each powered by an MAN B&W 50-bore ME-LGI main engine running on Methanol. The ME-LGI concept is also applied for operation on LPG. However, due to the large variations in gas quality and the low bulk modulus, an optimised design of the ME-LGI concept is used for this fuel type. MAN D&T has developed a wide range of Dual-Fuel engine technologies with the ability to operate on all alternative fuels available today and in the future. MAN will continue to be innovative and develop the portfolio of competitive Dual-Fuel engines, which can be cost-optimised for manufacturing. In addition, the company will further develop the equipment and specifications of auxiliary systems in support of achieving a cost-efficient installation of the dual-fuel engines in the vessels of the present and the future.
ME-LGI Methanol
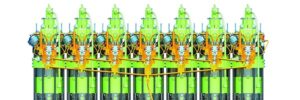
Operation on Methanol has become attractive for Methanol carriers operating in SECA areas. With the Sulphur-free fuel already on board, utilization of a Dual-Fuel engine is a natural choice. The first contracts for engines were obtained in 2013 – in total, seven vessels have been ordered for operation on Methanol. Methanol is well-suited as engine fuel for Diesel engines and, similar to ME-GI, the two-fuel injector approach is the one chosen for the ME-LGI engines.In line with the frequently used development process, a number of concept verification tests were performed at MAN’s Diesel Research Centre in Copenhagen. One cylinder on the research engine was converted to operate on Methanol in order to verify the combustion process and system design. This also involved the development and installation of a complete Methanol storage and handling facility with an LFSS similar to the one to be installed on the vessel. In continuation of the test in Copenhagen, tests were carried out at Mitsui Engineering and Shipbuilding on their four-cylinder test engine, which for this purpose had been converted to Methanol operation. Since then, three vessels have completed sea trials. Fig. 1 shows the first methanol carrier from Minnaminippon fitted with an MAN ME-LGI engine.
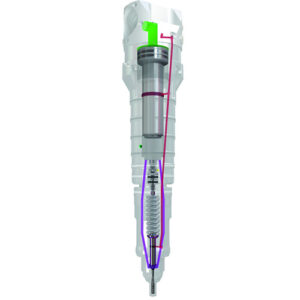
ME-LGIM injection system
The MAN ME- LGI engine concept for operation on Methanol is designated ME-LGIM and is based on the conventional electronically controlled ME engine with the following functional add-on parts (see Fig. 2):
* Unit injectors – the so-called LGI fuel booster injection valves (FBIV-M) for the injection of Methanol into the combustion chamber around TDC.
* Hydraulic control systems that control the LGI fuel booster valve operation.
* Sealing oil supply ensuring that no Methanol leakages occur in the moving parts of the Methanol injection system. A separate cooling and sealing oil unit handles the cooling and sealing oil on the engine.
* Double-walled piping to distribute Methanol to the individual cylinders.
* Draining and purging system for quick and reliable removal of Methanol from the engine.
* In addition to the engine control system, a safety system monitors the Methanol injection and combustion and ensures that the engine is taken back to Diesel oil operation in case of alarms.
* Fuel valve train for safe block-and bleed function between the supply system and engine.
* Fully automated Methanol supply system with embedded purge system.
The base engine is not significantly changed, apart from making room for the additional fuel system in and around the cylinder covers, and thus all the aspects of a standard MAN two-stroke diesel engine also hold true for an LGI engine. This includes options to optimize the engine layout for high load or part load to derate the engine and to combine the engine with waste heat recovery systems. Since the LGI is an add-on to the electronically controlled ME engine, converting an existing diesel engine into a dual-fuel engine capable of using both diesel and, for example, Methanol is possible. The diesel fuel system is not significantly altered on an LGI engine compared to a standard ME engine. As is the case for the ME-GI, the ME-LGI fuel system can change over to fuel mode, burning Diesel Oil or HFO from one stroke to the other without any limitation in speed or load.
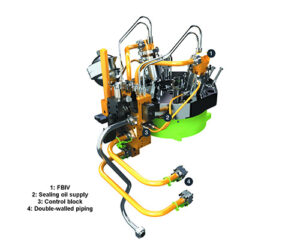
ME-LGI FBIV
The ME-LGI system utilizes the fuel booster injection valve (FBIV-M) shown in Fig. 3. The FBIV is designed as a batch-injector, combining a hydraulically actuated plunger pump with a spring-held injection needle valve that opens at a given fuel pressure.
Performance results
Functionality tests of LGI sub-systems and the initial performance tests were conducted on the 4S50ME-T9 test engine at Mitsui’s Tamano shipyard in Japan in the spring of 2015. In accordance with this, the layout of the four-cylinder test engine was matched as close to the later production engines as possible. The 4S50ME-T9 test engine at the Mitsui shipyard was the first two-stroke MAN engine to be operated entirely on Methanol in LGI mode. The engine was equipped with an extensive measurement setup for the duration of the tests.
Pilot oil consumption
The amount of pilot fuel is targeted to be around 5% of the MCR fuel oil consumption in Diesel Oil mode. The amount of pilot oil needed for securing ignition of the injected Methanol is very small. It is, however, a technical challenge to design a robust injection system that is large and powerful enough to enable fuel-efficient high-load operation on fuel oil, while being small and fast enough to be able to inject minute amounts of pilot oil in LGI operation.
In conclusion, it is not the requirement for secure ignition of the Methanol that sets the lower limit for pilot oil amount, but the minimum amount of fuel oil that can be reliably injected by the fuel oil injection system setting the lower limit for pilot amount. Tests showed that Methanol is a good Diesel engine fuel giving roughly 30% lower NOX emissions and slightly better SFOC (specific fuel oil consumption) compared to Diesel Oil operation when operating with identical thermodynamic operating points.
In conclusion, both NOX and SFOC targets are easily reached when employing Methanol as a fuel. As such, this finding is absolutely an excellent starting point for overall optimization of the engine performance.