Alarming deficiencies in lack of machinery knowledge on board of seagoing vessels
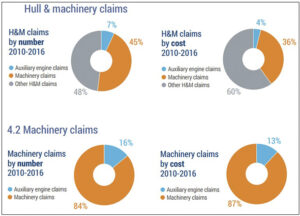
This report has been created by the Swedish Club, a marine mutual insurer with headquarter in Gothenburg Sweden, in response to concerns over damage to auxiliary engines. Its objective is to investigate auxiliary engine claims, highlight predominating factors and provide advice with a view of reducing the frequency/severity of auxiliary engine damage.
This report aims to shine a light on the important issue of damage to auxiliary engines, a significant segment of machinery claims – both in number and cost.
Auxiliary engines run at high revolutions and have a common lubrication system for both cylinder and crank case lubrication. Auxiliary engines are not under the same strict regime from the classification society and maintenance is often carried out by the vessel crew.
The Club has seen all too frequently the following causes of damage:
- Incorrect maintenance and repairs
- Failure to adhere to repair procedures and use of incorrect tools
- Crew lacking formal engine specific training
- Inexperienced crew and no expert in attendance
- Failure to detect contamination due to poor lubrication oil management
- Not following up on results from lubrication oil sampling
A few interesting data to consider:
Auxiliary engine claims account for 13% of the total machinery claim costs and 16% of the volume, with an average claim cost of USD 345,000.
The frequency for auxiliary engine claims is approximately 1.2% and has been relatively steady for the last few years.
Container ships have a higher claim frequency and cost in relation to fleet entry.
Approximately 50% of all auxiliary engine damage occurs immediately after maintenance work.
Incorrect maintenance and wrongful repair are the most common causes of damage.
Poor lubrication oil management is also a major contributing factor to auxiliary engine break downs.
Do it right – or don’t do it at all
Reviewing the Clubs records they noted that the common factor for these occurrences in most cases is the incorrect assembly of vital engine parts in connection with regular overhaul. In particular, the assembly of connecting rods, bearings and pistons causes severe and costly accidents.
- Non adherence to procedures, lack of training and experience are major factors. A connecting rod assembly is a critical and highly stressed joint and must be re-assembled exactly in accordance with manufacturer’s instructions with proper tools. All too often the Club sees insufficient understanding of the importance of the procedures.
- Special hydraulic tools are often used for the engine assembly. These tools must be treated with care and need to be calibrated and carefully checked before use.
- The manager has the responsibility to ensure that crews are competent to undertake such repairs/overhaul. The crew should either be trained on the specific engine types or alternatively, an expert from the manufacturer should be engaged to attend the overhaul.
Lube oil – the root of all evil
Poor lubrication oil management is in many cases the predominating factor for an auxiliary engine breakdown.
Auxiliary engines are 4-stroke engines and as such the engine oil is used for cooling of pistons crowns and lubrication of cylinder liners, bearings, etc. There is an apparent risk that the lube oil will be contaminated with soot and combustion particles, especially if the engine has accumulated some running hours. Proper lubrication oil management is critical for minimising the risk of engine failures. This is essential when operating the engine on heavy fuel oil (HFO). The lubrication oil must be analysed at regular intervals.
Detection of water, soot particles, metal particles, etc. will serve as an early warning for engine problems. Negative results from oil analysis must be investigated
and addressed promptly.
Best practice
Whilst prevention is always better than cure, steps can be taken to mitigate the damage caused by the failure of the auxiliary engine. Most modern auxiliary engine installations can be started and stopped remotely from the engine control room. It is good practice to be always present at the engine when starting the same, especially after longer periods of still-stand and after overhaul. During start-up, if anything goes wrong, it usually happens very quickly. If someone is present at the engine there is at least a possibility to intervene and shut down the engine manually.